完全受注生産で進まないカイゼン
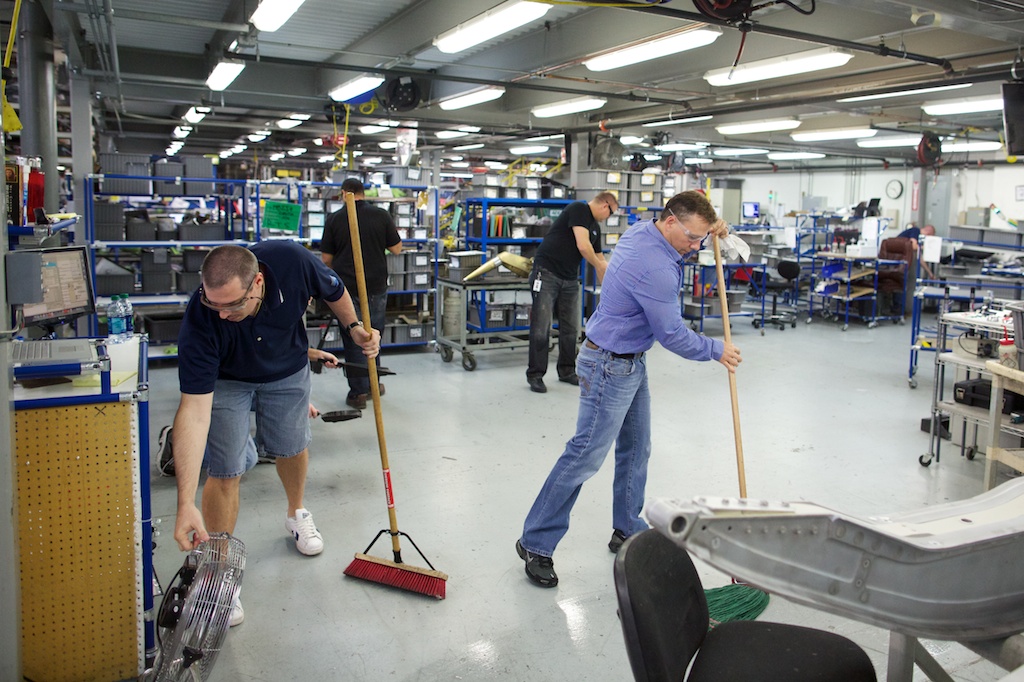
アメリカにある航空部品修理会社A社では、ジャンボジェット機やヘリコプターなどの航空機からメンテナンスのために外された使用中の部品が、世界中から送られて来ます。通常はそれを一品ずつ、どこが摩耗していて修理するのかを検査をして見積もりを出し、客先の承認を経て修理作業に入り完成するまでに1か月から2か月かかるのが業界の常識でした。
しかしこの会社では「2週間で完成します」と短納期を売りにしており、 世界中から送られてくる修理部品は毎年増え続け、それに伴い従業員も増え続け、300人を超えました。人数が増えるにつれて工程間が伸びていき、また管理する仕掛品の数が多くなりました。1品ごとに修理項目が異なる完全受注生産のためにカイゼンしようにもどうしたらいいか悩んでいました。
カイゼンは掃除から
始めに行ったカイゼンは、掃除をすることでした。モノの置き場を決めるのにラインテープを貼るのですが、そのためには床をほうきで掃き、キレイにすることから始めます。掃除をしようとすると「掃除は専門の人がいる、彼らの仕事を奪ってはいけない」と言われました。「カイゼンは誰かにやってもらうものではなくて、自らより善くかえることです。だから私は自らやります」とほうきを探してきて掃除を始めました。すると幹部も一緒にやり始め、ついには全員で床を掃き掃除しました。
掃除をしたことがない彼らは、ほうきを逆手に握って慣れない手つきで一緒に汗をかきながら掃除をしました。掃除をしてキレイになった床に皆で車座になって座りました。はじめて自分達の職場を掃除した仲間は「やったぞ!」と自然と笑顔になりました。
見える化でカイゼンしやすい職場
掃除をしたら、仕掛台車の位置を決め、テープで定位置管理をしました。表示をして、必要数を決めました。多い分は前工程に戻し、工程間の仕掛品を減らしていきました。
ここで問題がおこりました。前工程と後工程が1対1になっておらず、乱流になっていました。修理部品は1品ごとに修理箇所がことなり、そのために修理工程も同じ流れではなく、何度も加工する、同じ工程を行き来することがあるために工程間の仕掛品が定まりませんでした。
そこですべての仕掛品に次の工程に運んだら、処理時間をもとに何時に投入されるか記しました。「13:00」「13:30」「14:30」「16:00」と投入時間を見える化しました。まずは工程待ちを4時間に設定し、4時間分を超えた場合は、他の工程から応援に来て早く処理するようにしました。そのためにスキルマップ(多能工訓練表)を壁に貼り、積極的に教育訓練を進めました。
すると工程間に仕掛品が停滞せずに、次々に流れるようになりました。
多能工訓練で加工ミス70%削減
これまでは受注増に伴う人材採用「誰でもいいから即採用」では、スキルのない人でもラインに入れて教えていたため、どうして加工ミスが起きており、毎年加工ミスによる損失金額が膨れ上がってました。
しかしスキルマップを壁に貼り、不足しているスキルが誰でも見えるようになったことでスキルの習得を競い合い、教え合うことでチームワークが上がりました。すると毎年増え続けた加工ミスは70%減少し、加工コストが大きくカイゼンされました。
毎年増え続ける受注増の中、初めて人員減少に転じる
さらに、売り上げ増に伴い毎年増やし続けた従業員数が初めて減少しました。現場のカイゼンが進んだことで、各工程の負荷が把握できるようになり、また作業者のスキルが上がりました。その結果、新たに採用しなくても受注増をこなせることがわかり、自然減で従業員数が減少に転じたのです。
最高益を更新
この会社は過去最高益を更新し、全従業員が過去最高額のボーナスをもらうようになりました。
「カイゼンで皆が笑顔に!」を実感した瞬間になりました。
加工ミス 70%減少
毎年増やし続けた従業員数が初めて減少し、過去最高益を更新