収穫期に倍増する従業員数
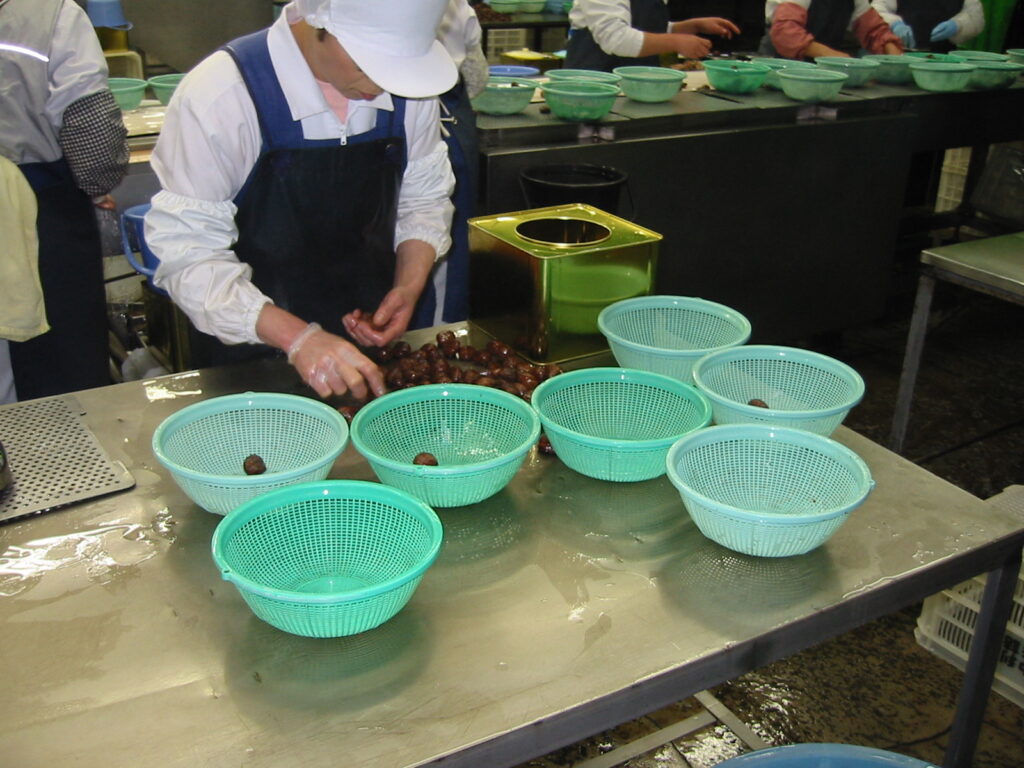
食品製造業B社では、秋になると収穫されたばかりの果物が毎日入荷されてきます。そして缶詰用の果物は、鮮度が高いまま缶詰に入れて加熱殺菌されます。その処理のための、閑散期の従業員数と同数の従業員が、作業訓練の期間も入れて6か月間雇用されていました。
そのため6か月間は従業員数が倍になり、活気に満ちていました。経営者から、「カイゼンを取り入れて従業員がやりがいをもって仕事に取り組んでほしい」と依頼がありました。
コンベヤーは遅い方が生産性が上がる
工場に足を踏み入れると、洗浄工程、選別工程、包装工程といたるところにコンベヤーベルトがありました。 分業をして短い時間で処理をするベルトコンベヤーは 、季節雇用の従業員に教える方も教わる方も負担が少なく、とても効率が良いようにみ思われていました。
しかしコンベヤーによる分業生産では、各作業の作業時間のバラツキのためにおこる「手待ち時間」があり、コンベヤーのスピードが早く処理量が早いほど、手待ち時間による生産性ロスが起ここります。たとえば3秒のラインスピードで流すした時に、手待ち時間がわずか1秒であった場合でも、手待ち時間の割合はなんと33%になります。それにもかかわらず、1秒の手待ち時間はほとんどの場合、使うことができないのです。
そこで前後工程を覚えた多能工を育成し、手待ち時間を極力なくすようにします。そのためには、ラインスピードをできるだけ遅くし、手待ち時間を集めて隣の工程を取り込みやすくします。食品工場ではコンベヤースピードをできるだけ早く最大能力で運用しており、ラインスピードをできるだけ上げる、といった工場が多くあります。
そこで一日の必要数で稼働時間を割って求めた数字をもとに、ラインスピードを出すと、ラインスピードは20%から30%遅くできるラインが多くあります。この工場でも必要数からラインスピードを割り出すことで包装ラインでは、コンベヤーは30%遅くすることができました。その結果、包装ラインでは作業人員が30%少なくても同じ数量ができるようになりました。
選別工程で一人屋台工程を導入
選別工程でもコンベヤーベルトを使っていました。果物をサイズ別に分けるために、作業者は一人ずつSサイズ担当、Mサイズ担当、Lサイズ担当、LLサイズ担当に分かれており、自分のサイズの果物だけをコンベヤーから取り出し、かごの中に入れていました。
ところがSサイズと思って手にとっても、大きい場合はコンベヤーベルトの上に戻していました。そのために同じ果物がコンベヤーを流れる中で何度も手に取って戻されるムダがおこっていました。さらに果物はサイズがバラバラなので、手待ち時間がありました。
選別終了後にコンベヤーベルトを洗浄するのですが、全体が汚れるためにコンベヤーの上だけではなく、側面、裏側まで洗う必要があり、30分かかっていました。
そこで一人屋台方式で選別を行うことにしました。果物1個を手に取ったらサイズを判断し、Sサイズ、Mサイズ、Lサイズ、LLサイズのカゴに入れる1個流し作業を1人で行うようにしました。始めはなれず戸惑っていましたが、すぐに慣れて次々にサイズ別のカゴに入れていくようになりました。すると手待ち時間がなくなりました。
さらに選別終了後の洗浄は、ステンレスの作業台の上にバケツの水を流して終わるため、わずか5分で終わるようになりました。
その結果、選別工程は1/2の作業人員で作業ができるようになりました。
工場全体にカイゼンを広め、生産性200%を達成
同じようにカイゼンを進め、工程をつないでムダな運搬をなくすなど全社にカイゼンを進めた結果、なんと収穫期の繁忙期でも臨時雇用の従業員を採用する必要がなくなりました。その結果、生産性200%を達成しました。
経営者の方は「従業員の活性化のために導入したカイゼンでしたが、まさかここまで効果が出るのに驚きました。毎年忘年会は臨時雇用の従業員も一緒になって閑散期の2倍の人数で行っていたため大人数でした。しかしその必要がなくなったために忘年会がこれまでの半分でおこなったため、さびしかったです」と言いながら、とても笑顔で語ってくれました。
繁忙期でも臨時雇用の必要がなくなり、生産性200%達成