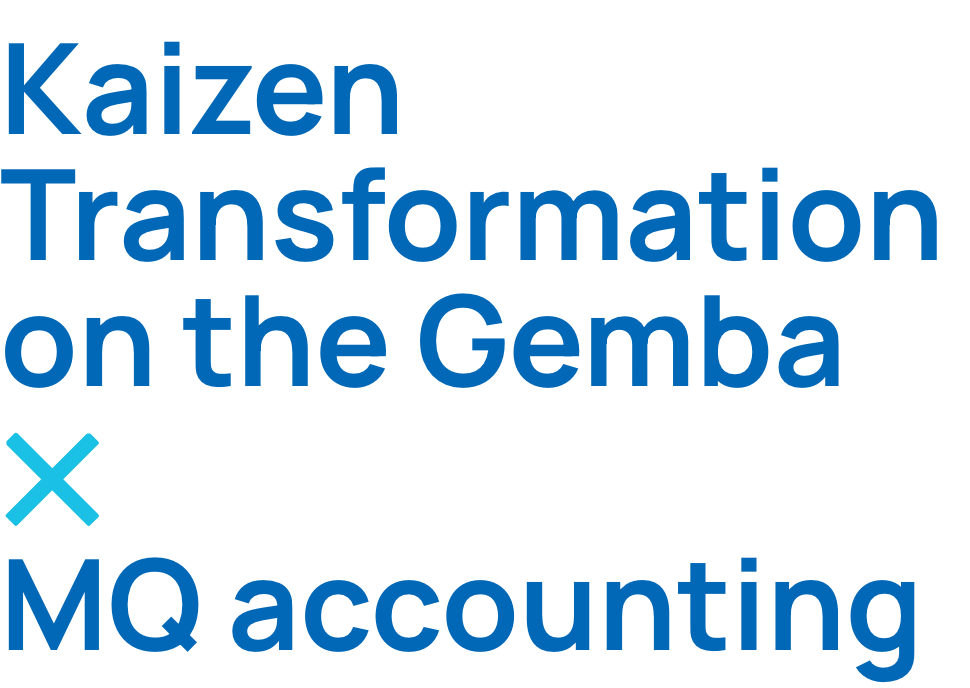
Through Kaizen utilizing the Toyota Production System and MQ Accounting (Added Value MQ > Fixed Cost F), we can turn Kaizen effects into profits.
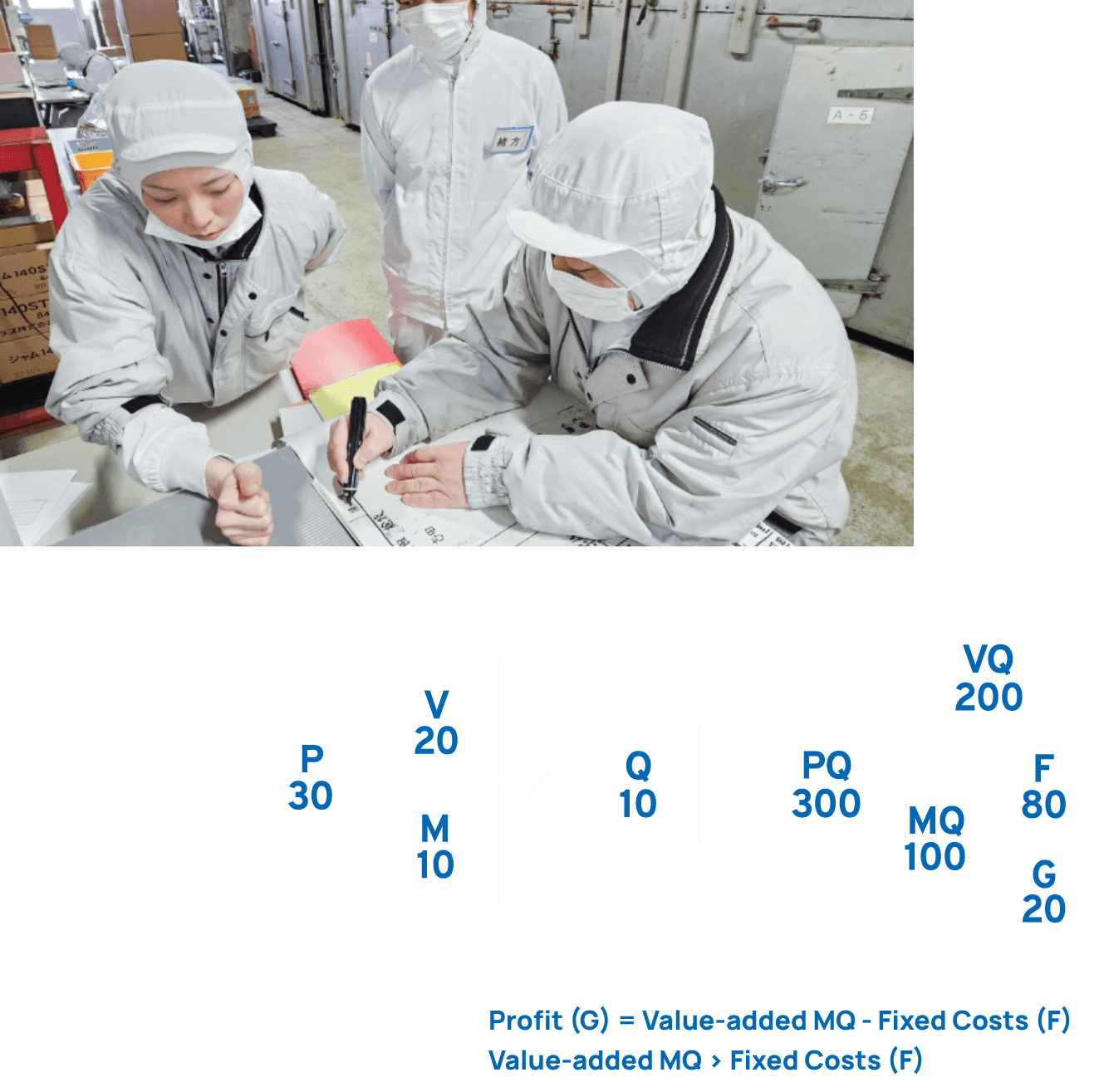
Solutions
Solving problems with 5S,
Kaizen,and MQ accounting
- Increasing Productivity
- Reducing Lead Time
- Reducing Inventory
- Eliminate Personal tasks
- Increasing Profits
- Developing Employees who think and act
Kaizen is to change actions for the better
Kaizen based on the Toyota Production System
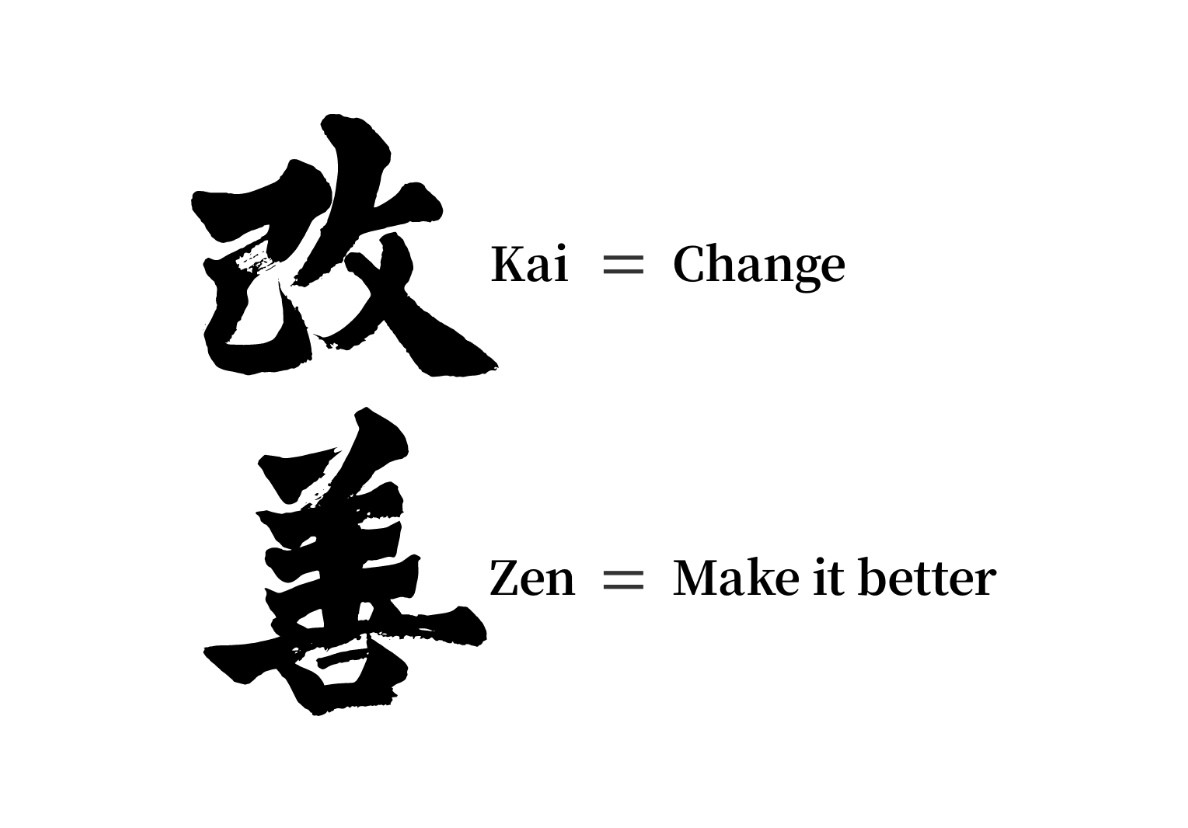
Kaizen is something can be done by anyone. All you have to do is act to change whatever you want to something easier or faster.
Reasons
Why people choose GENKI LEADERSHIP?
01
Shocking Speed
Change immediately, change on the spot!
We go to the site and work on kaizen right there and then. The speed at which we work allows you to feel the effects right away.
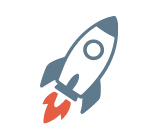
02
Ongoing support until success
Kaizen is something anyone can do.
Our motto is “① Show them how to do it ② Do it together ③ We can do it ourselves,” and we will work with you to grow while keeping our eyes on you.
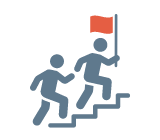
03
Turn Kaizen results into tangible profits
Using MQ accounting, we reverse-engineer how much Kaizen is needed to create profit—transforming operations and management alike.
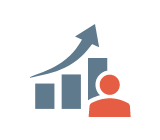
04
We promote Kaizen through MG and TOC training.
Company-wide engagement in Kaizen leads to greater outcomes.
Our MG and TOC training programs foster shared understanding across teams and enhance the momentum for continuous improvement.
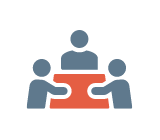
Not just theory—Kaizen in action
Kaizen That Works
- Kaizen in the Workplace
- Kaizen in Management Drives Greater Results
- MQ Accounting for Strategic Business Results
1. Kaizen in the Workplace
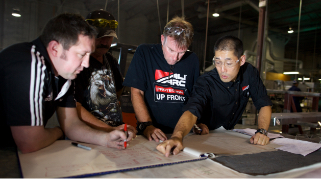
There are two types of Kaizen: “point Kaizen” and “line Kaizen.”
Point Kaizen refers to localized improvements made within each workplace—something every employee can take part in.
This includes 5S activities, eliminating even one second of waste, reducing unnecessary motions, improving work processes, and minimizing work-in-progress inventory.
We also promote initiatives such as multi-skilled cell production, the one-person cart system, and one-piece flow production.
Line Kaizen focuses on creating a smooth flow from the arrival of raw materials to the shipment of finished products.
The improvement process begins at the final stage of production, where we capture customer needs and then work backward through upstream processes.
By synchronizing each step along the production line, we reduce work-in-progress inventory, shorten lead times, and minimize stock levels.
Furthermore, teams across different stages and departments support one another, practicing a people-centered approach to bring out the best in every individual.
2. Kaizen in Management Drives Greater Results
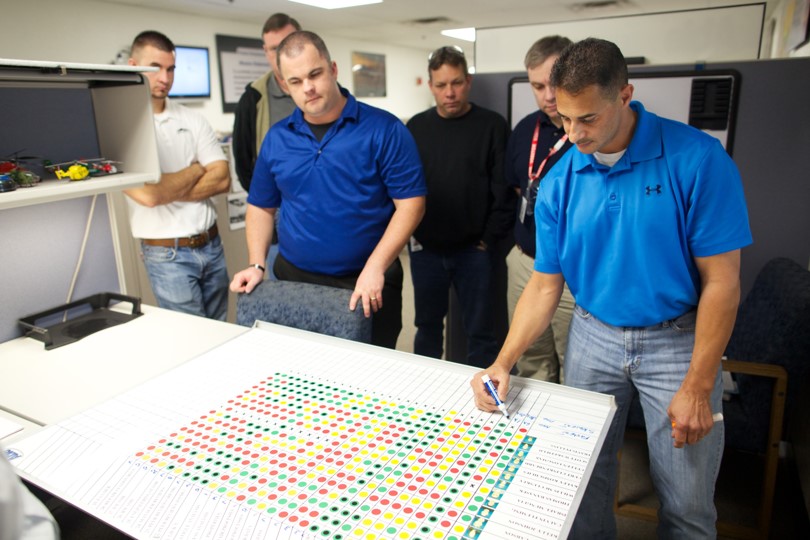
To achieve meaningful Kaizen results, visualization is essential.
We focus on visualizing production management so that the workplace can take ownership of it.
By upgrading from simple scheduling to time-based management, we enable better synchronization between processes, which leads to shorter lead times, reduced work-in-progress, and lower inventory levels.
To truly improve productivity, we evaluate not by daily output alone, but by labor-hour productivity—output per person-hour.
When frontline teams manage their time on their own, they gain visibility into process loads and equipment utilization.
This, in turn, promotes mutual support through multi-skilled workers, encourages people-focused improvement (Katsujin), and helps enhance overall productivity.
We also extend Kaizen effects by addressing bottlenecks, solving labor shortages, and promoting in-house production where possible.
3. MQ Accounting for Strategic Business Results
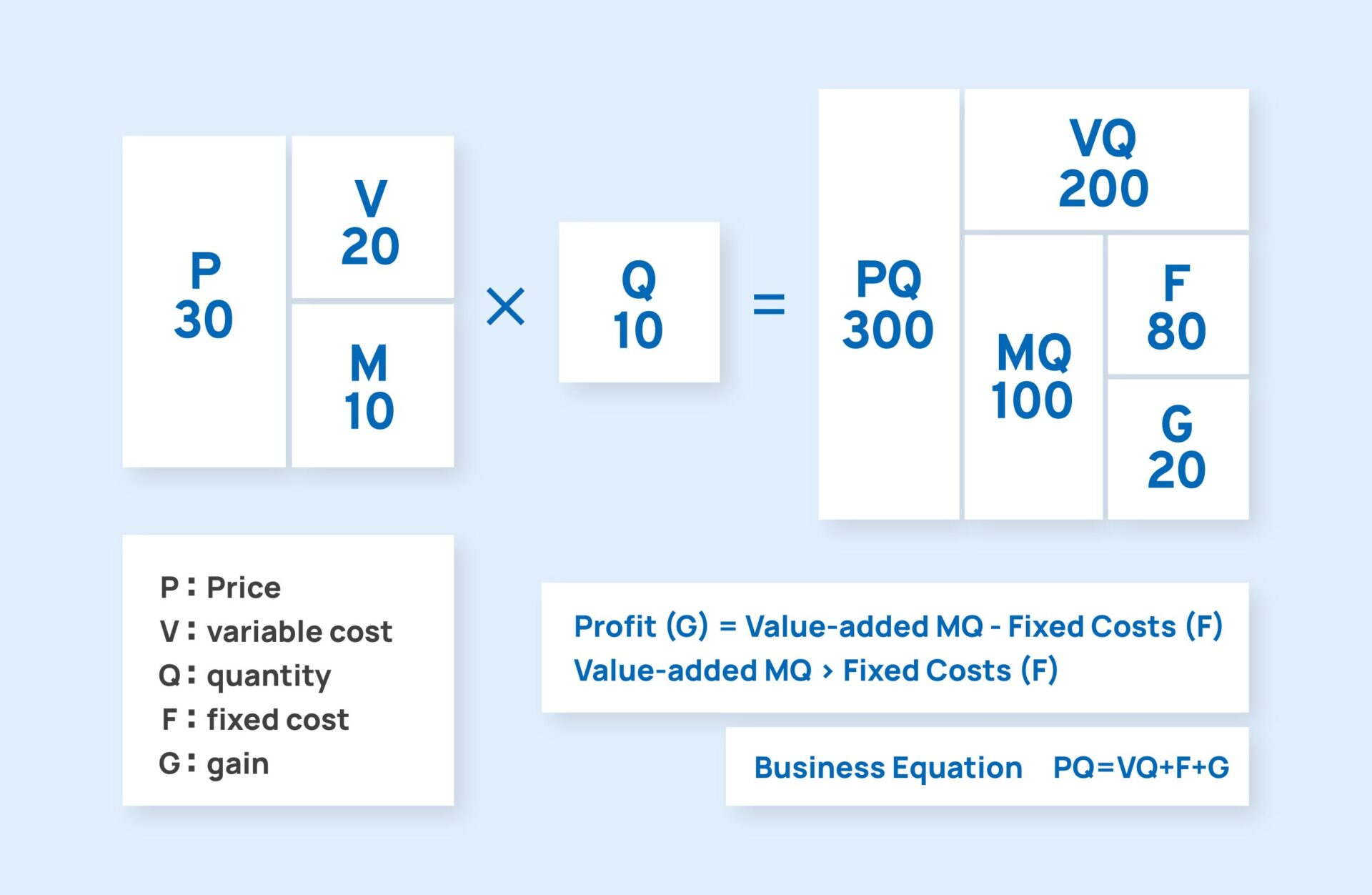
MQ Accounting uses visual tools to help even those without a background in bookkeeping or accounting intuitively understand how profit is generated.
The idea that “increasing sales leads to higher profits” is not always correct—it’s possible for sales to grow while still operating at a loss.
By understanding the four key elements of MQ Accounting, known as the “business equation,” one can clearly see what is truly needed to increase profit.
Through value-added analysis by customer and by product, it becomes easy to identify which customers and products contribute to profit—and which do not.
In addition, improvements in productivity can be linked to strategic decisions such as developing new customers, launching new products, or bringing production in-house—making it easier to create effective business strategies.
Where continuous improvement begins
The Kaizen Mindset
5S

By thoroughly practicing 5S, we create a workplace where waste, problems, and abnormalities are easier to notice.
Sort (Seiri): Discard and Return
Separate what is necessary from what is unnecessary, and discard the unnecessary items.
Even if something is not needed at that particular site, return it to its proper storage location if it must be kept.
Set in Order (Seiton): Make it Visible
Display necessary items so they are easy to access and use.
This eliminates the waste of searching.
Visual management should follow the “Three-Fixed Rule”: fixed items, fixed locations, and fixed quantities.
Shine (Seiso): Sweep and Wipe
By thoroughly cleaning—sweeping and wiping—we help both people and equipment perform at their best.
Regular cleaning also makes it easier to notice equipment abnormalities, leading to effective preventive maintenance.
Standardize (Seiketsu): Create Systems
Seiketsu means maintaining the results of the first three S’s—Sort, Set in Order, and Shine.
While those actions can be done on the spot, if the condition falls apart the next day, cleanliness is not truly achieved.
To sustain improvements, we build systems.
We clearly define who does what, when, where, and how—and ensure it is done consistently.
Discipline (Shitsuke): Build Good Habits
Shitsuke means developing the habit of following established rules.
When good practices are carried out consistently over time, they become part of daily routine.
Following rules also means that safety procedures and work standards are upheld—leading to fewer injuries and defects, and ultimately improving both safety and quality.
Change Words and Actions
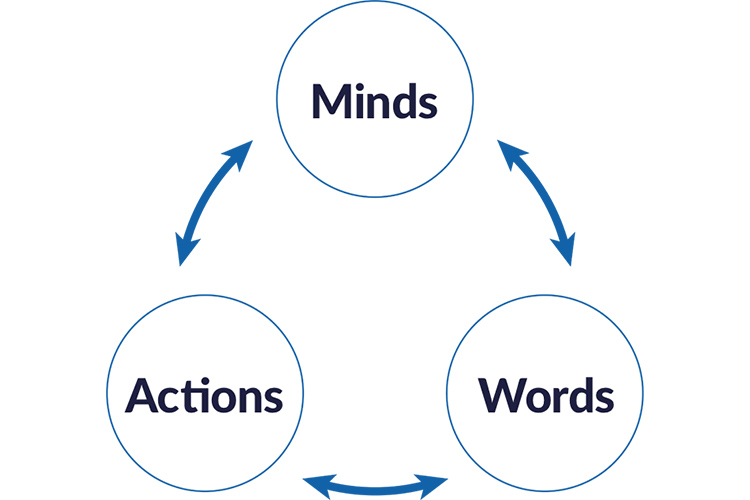
Change your words and actions, and your mindset will follow.
It is often said, “When the mind changes, actions change; when actions change, habits change.”
But in reality, a person’s mindset does not change easily.
To truly improve ourselves, we must first reject yesterday’s ways—and take action to create something better.
Changing your words means choosing language that leads to action and expresses a positive attitude.
For example, instead of saying “I think it might be good to try…,” say “Why don’t we give it a try?”
Rather than simply saying “I understand,” say “I’ll do it!”
Changing your actions means doing things immediately—like picking up trash when you see it, cleaning without being asked, or trying out a good idea as soon as it comes to mind.
Rather than trying to change the invisible “mind,” Kaizen begins by changing the visible—our words and actions.
Through this process, the mind will naturally begin to change as well.
One Step by 100 People Rather than 100 Steps by One Person
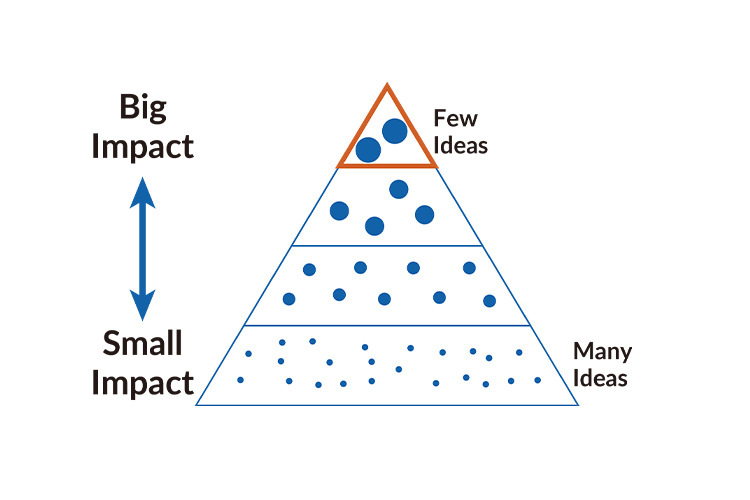
If you focus only on achieving big results through Kaizen, it can be difficult to sustain improvement over time.
Think of it like a pyramid—big results are just the small triangle near the top.
The real power of Kaizen comes when everyone is involved, not just a few.
By encouraging even the smallest steps—like a one-second improvement or a single action anyone can take—we begin to build the solid foundation of the pyramid.
That’s where true, lasting change begins.
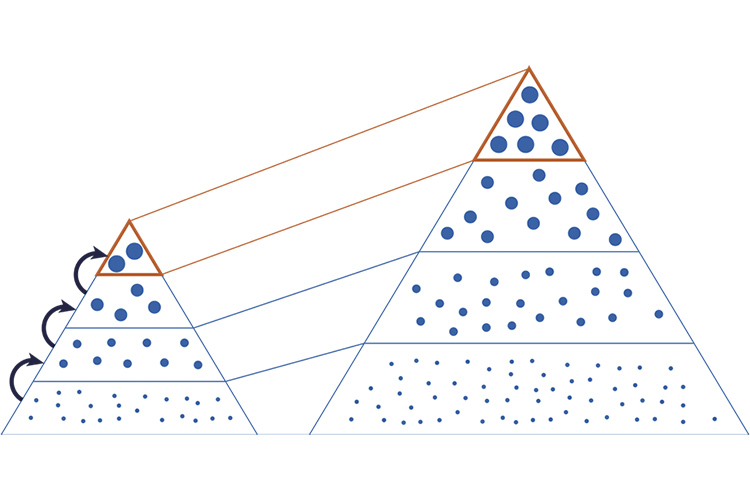
By starting Kaizen from the final process and improving management practices, we can create a greater impact—not only within one’s own workplace, but also across upstream and downstream processes, and ultimately for the customer.
The more people who develop the ability to notice and the courage to take action through small Kaizen steps—just one second, one step at a time—the greater the capacity for large-scale improvements becomes.
A strong foundation built on many small improvements leads to more significant Kaizen achievements at the top of the pyramid.
Kaizen is not something reserved for a select few “experts.”
It is a practice carried out by the people who know the worksite best—those who create value on the front lines.
Through their actions, they improve their own workplaces and contribute to transforming the company for the better.
The beliefs behind our actions
Our Philosophy
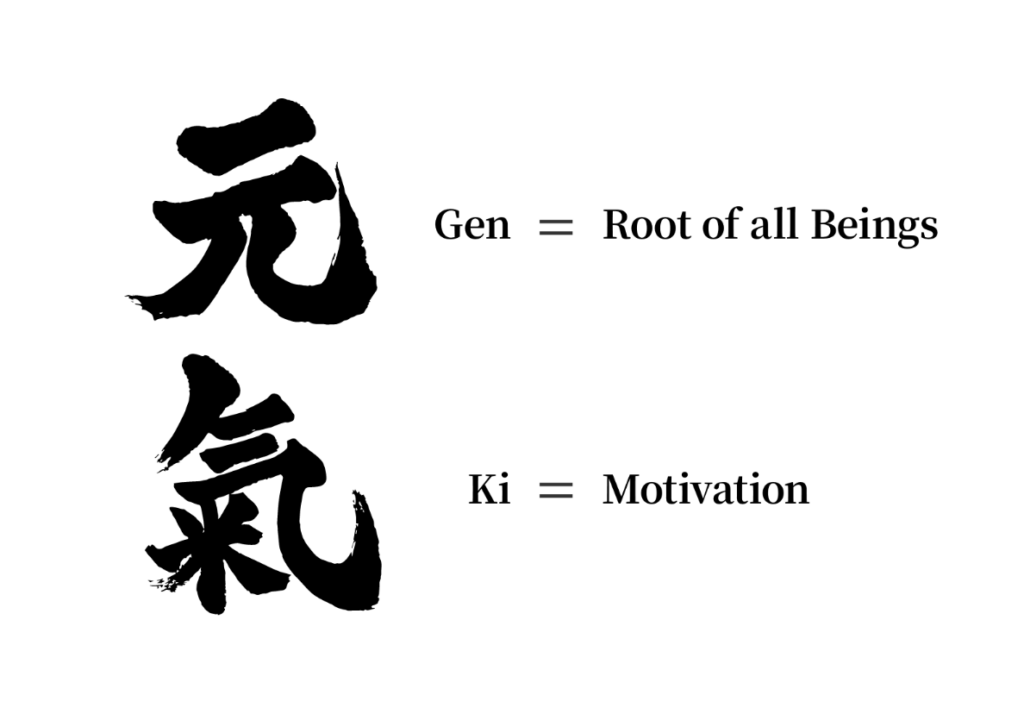
“Genki” refers to the vital energy that forms the foundation of all creation. It is the essential force that drives both mind and body.
Our Aspiration
Building Energetic
People
We nurture proactive and energized individuals who can recognize challenges on their own and take initiative to act.
Building Energetic
Workplaces
We create workplaces filled with energy, where people feel the joy of working and customers feel truly cared for.
Building Energetic
Companies
We build vibrant, healthy companies by combining on-site Kaizen with MQ accounting.
We address business challenges through on-site Kaizen rooted in the Toyota Production System, and connect those improvements to profit using MQ Accounting (Added Value MQ > Fixed Cost F).
Essential facts about our company
Company Profile
Company name | GENKI LEADERSHIP |
Founder | Toshihiko Miura |
Business | Kaizen Transformation based on the Toyota Production System |
Address | 3-7-11-4, Nagatoishi, Kurume, Fukuoka, 830-0027, JAPAN TEL : +81-942-80-8364 |
support@genkileadership.com |
Profile
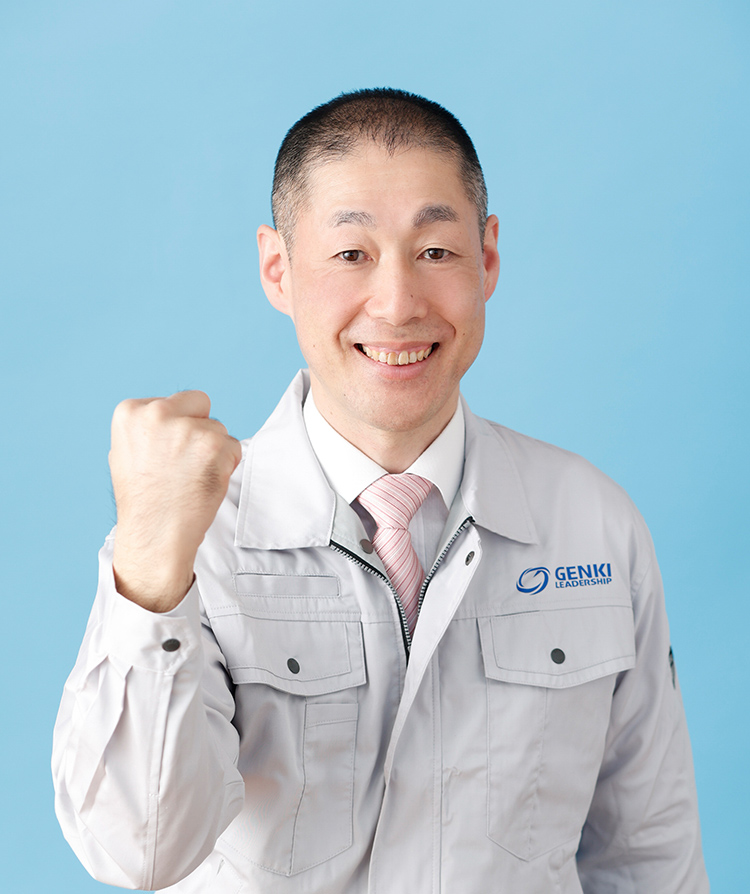
A “Super Genki” partner who inspires action and works with you to transform the workplace.
Toshihiko Miura
President, GENKI LEADERSHIP Inc.
1997
In 1997, I joined the PEC Industrial Education Center (now the PEC Association), led by Mr. Hitoshi Yamada, who introduced the cell production system to Sony and Canon. There, I began my journey as a Kaizen consultant, specializing in waste elimination through the Toyota Production System.
I have put Kaizen and waste-reduction practices into action in a variety of industries, including manufacturing (food, furniture, semiconductors, electronics, metal processing, automotive parts, mold making, and more), logistics warehouses, and food supermarkets.
Rather than offering advice from a conference room, I take a hands-on approach—working directly at the site to transform the workplace and, ultimately, the business itself.
At one company with annual sales of 3 billion yen, our efforts led to the first return to profitability in ten years.
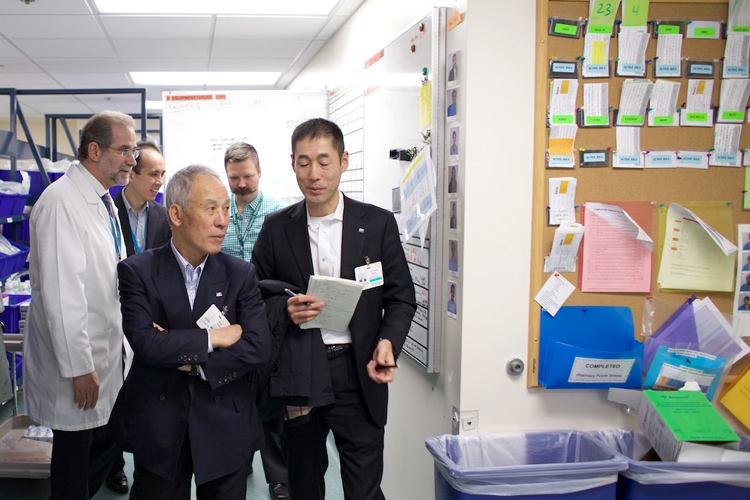
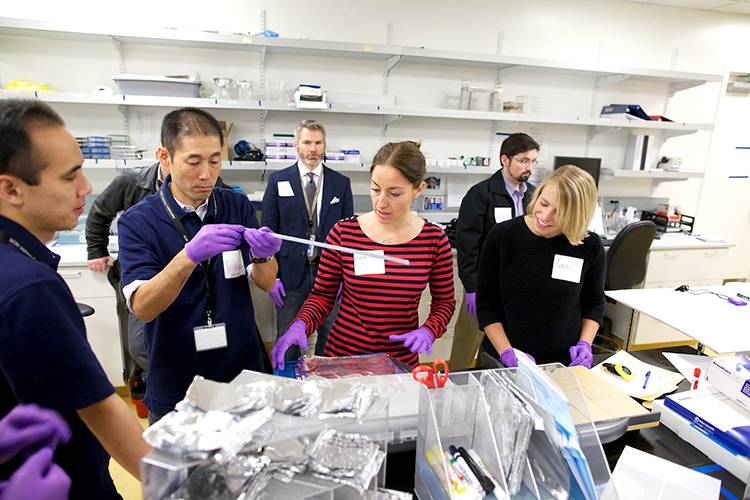
2000
In 2000, I participated in the MQ Strategy Game (MG) hosted by Dr. Junichiro Nishi, the founder of MQ Accounting and director of the Nishi Institute.
It was there that I met Mr. Takeshi Tsuda and began studying human sciences.
2005
In 2005, I founded Genki Management.
Continuing under the guidance of Dr. Hitoshi Yamada, I worked as a dedicated instructor at the PEC Industrial Education Center, where I actively implemented and expanded the Toyota Production System.
2007
In 2007, my book “Simple Waste Elimination Pocketbook” (published by Nikkan Kogyo Shimbunsha), which compiled real-life examples of waste reduction from the workplace, was released.
It sold so well that a second printing was issued just one month after launch.
To date, it has been reprinted nine times, with over 10,000 copies in circulation.
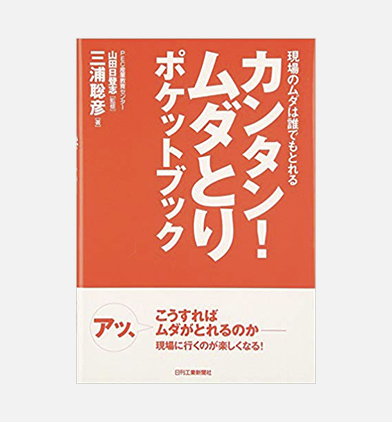
2011
In 2011, I completed the MBA program at Kyushu University Business School (Master of Business Administration).
While studying, I realized that “unless I understand global manufacturing, I can’t truly advise Japanese business leaders.”
That realization led to a personal mission: to revitalize Japanese manufacturing.
I began working overseas, introducing the Toyota Production System and Kaizen to local companies where no Japanese staff were present.
Since then, I have implemented these methods at over 30 companies in countries including the United States, Canada, Australia, New Zealand, China, and the Philippines.
In the U.S., a company in the aerospace component repair industry achieved its highest-ever profit one year after my guidance.
In the Philippines, a factory with 120 employees increased its productivity by an astounding 170% in just six months, leading to its first return to profitability in nine years.
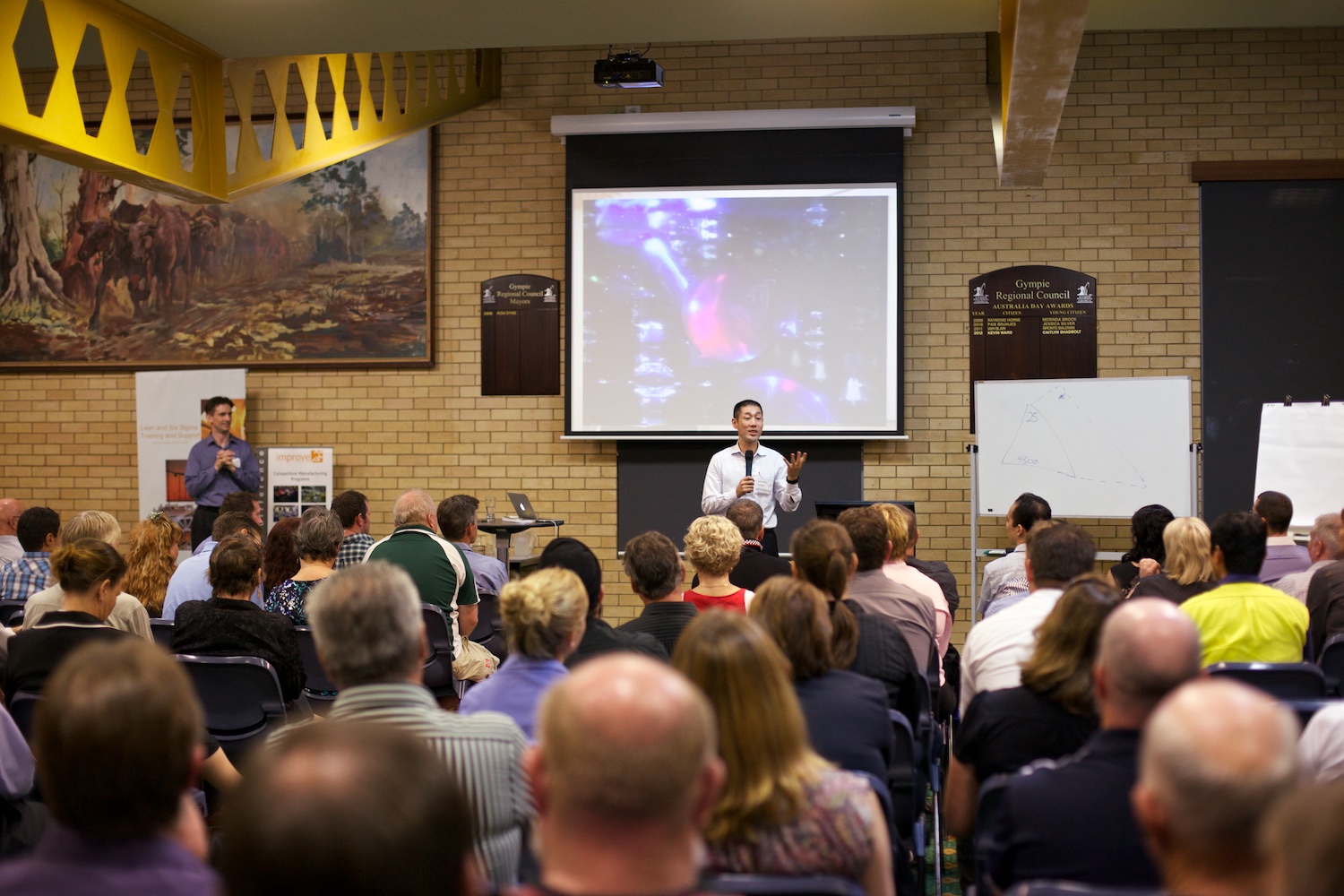
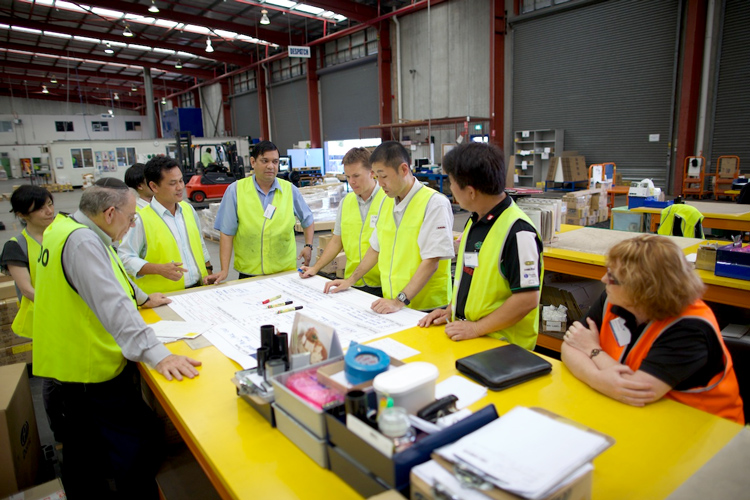
2017
In 2017, I co-authored True Kaizen: Management’s Role in Improving Work Climate and Culture (CRC Press), together with Collin McLoughlin.
The book compares Kaizen practices in Japan and overseas, and explores how on-site Kaizen can be effectively connected to management strategy—featuring a wealth of real-world case studies.
It has since been read by professionals around the world.
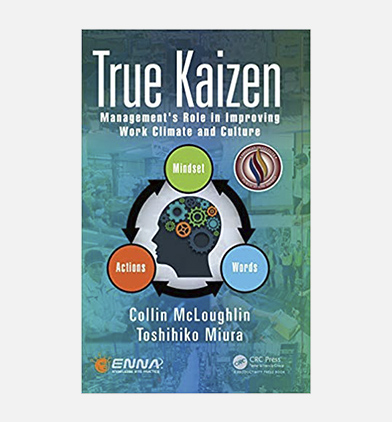
2019
In May 2019, True Kaizen was selected for the Shingo Publication Award 2019 by the Shingo Institute, an organization established in honor of Dr. Shigeo Shingo, who contributed significantly to the development of Single-Minute Exchange of Die (SMED) in the Toyota Production System.
2021
In 2021, I had the opportunity to reunite with Dr. Junichiro Nishi, the founder of MQ Accounting and director of the Nishi Institute, for the first time in 21 years. This reunion deepened my understanding and practice of MQ Accounting.
In July of the same year, I began a series titled “Theory and Practice: Kaizen Drills to Enhance Thinking Skills” in the Kaizen-focused magazine Factory Management (published by THE NIKKAN KOGYO SHIMBUN,LTD.).
Profile Summary
1997 | Joined PEC Personal Education Center (currently known as PEC Kyokai (PEC Association)) |
2007 | Publication of Simple and Effective! Waste Elimination Facilitator Guide (Kantan! Muda Tori Pocket Book), Nikkan Kogyo Shimbun, Ltd. |
2011 | Graduated from the Kyushu University Business School |
2017 | Publication of True Kaizen: Management’s Role in Improving Work Climate and Culture, Collin McLoughlin, Toshihiko Miura, CRC Press. |
2019 | Received the Shingo Publication Award 2019 Established GENKI LEADERSHIP |
2021 | Factory Management (published by THE NIKKAN KOGYO SHIMBUN, LTD.) “Theory and Practice: Kaizen Drills to Enhance Thinking Skills” (from the August 2021 issue to the July 2025 issue) |
Certifications & Licenses
- Certified MG Instructor (Authorized by Nishi Institute)
- Certified TOC Instructor (Authorized by Soft Power Laboratory)
- Certified TWI-JI Trainer (“Job Instruction”)
Degree
- Master of Business Administration (MBA)
Published Resources
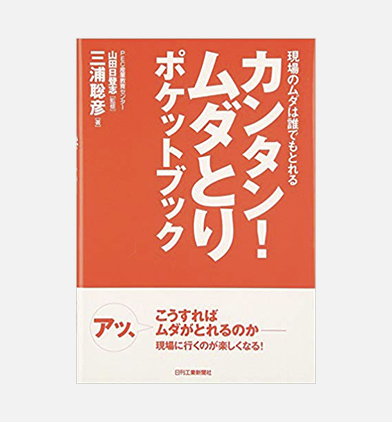
Simple and Effective! Waste Elimination Facilitator Guide (Kantan! Muda Tori Pocket Book)
by Toshihiko Miura, Nikkan Kogyo Shimbun, Ltd.
Target readers: Kaizen leaders and workers
This book explains the key points behind successufully eliminating waste directly on the Gemba. It contains more than 90 actual case studies from best-in-class organizations in Japan. Each case study illustrates the state before Kaizen and that after Kaizen in order to explain every detail of waste elimination techniques and the principles behind quantifying the financial performance increase after each execution in a simple manner.
To date, this book has been reprinted 10 times with more than 10,000 copies sold.
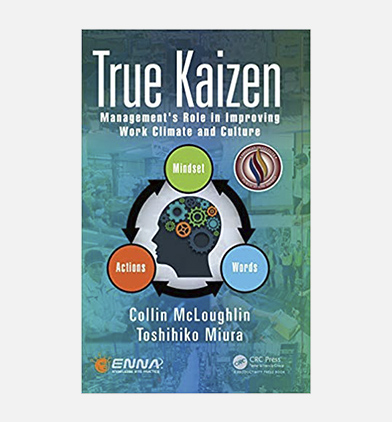
True Kaizen – Manager’s Role in Improving Work Climate and Culture
by Collin McLoughlin and Toshihiko Miura, CRC Press
Target readers: Top leadership executives, middle managers, supervisors, internal CI department consultants
Top-down Kaizen does not yield sufficient results without engaging the entire frontline workforce. This book advocates the “Cycle of Kaizen” to address the importance of strategic goals from the top that can be realized by the entire frontline workforce by refining the top-down and bottom-up Kaizen involvement.
The book explains how Kaizen is not something that can only be performed by people with special qualifications and training. Everyone can perform Kaizen can by first changing their words and actions which leads to a positive collective mindset. This book provides a number of case studies to prove that this is the right approach for engaging people.
True Kaizen also Provides readers with a number of case studies from 35 different organizations that have successfully introduced the Toyota Production System to their operations. These studies are supported by many easy-to-understand charts and figures, so the book is recommended for global audiences who wish to implement Kaizen in a more effective and sustainable manner.
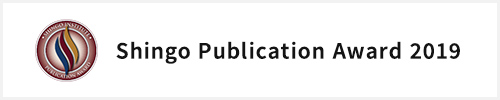